Let me take a moment to add a cautionary warning. Make sure you get a good drywall crew. I used cheap, and somewhat inexperienced labor and am paying for it every day now. Anytime I want to work on a room, I first have to fix the drywall mistakes, ugly seams, and mismatched edges. It is taking a lot of my time, and it is frustrating work. Don't skimp on this part of the job!
Sunday, August 30, 2009
Interior Framing
Let me take a moment to add a cautionary warning. Make sure you get a good drywall crew. I used cheap, and somewhat inexperienced labor and am paying for it every day now. Anytime I want to work on a room, I first have to fix the drywall mistakes, ugly seams, and mismatched edges. It is taking a lot of my time, and it is frustrating work. Don't skimp on this part of the job!
Sunday, August 23, 2009
Rough-Ins and Flooring
Once the shell is in place, your plans become even more important because it is all that you have to ensure that everything comes together with the different contractors that will do the rest of the work. Make sure you have spent the time to work out as many kinks as you can while still just putting it on paper. Unfortunately, unless you are building to the same set of plans you built to before, there will be some mistakes, or at least things that you wish you had done a little differently. We did spend a lot of time on our plans. I even entered them in my computer and created a 3D layout to do a virtual walkthrough. This was very helpful and I'm sure we avoided quite a few mistakes by doing that. We have been living in the house for 4 months now and I love the layout. My only regrets are that we did not realize we could not get DSL in our location, so computer usage requires ethernet lines that I did not plan for. I did, however, make sure there were lots of conduits to each room which did allow me to make the adjustments.

The large white pipes you see above are the drain lines. The red lines are the hot water, and the blue the cold. The gray pipes are electrical conduits. The strings were layed-out to indicate where the walls would be so everything lined up correctly.
This shot shows the white pipe used as air ducts. Notice the aluminum riser used to direct the air up through the floor. Notice also that the top of that duct would be the actual floor height.
Once everything has been layed out, the strings have been removed, and gravel added to bring the height of the floor up a bit, a layer of plastic and 4 inches of concrete are poured inside the shell. I was not able to be there for the whole process, and found out later that no stress relief cracks were added. Since concrete always cracks in large areas, the floor found it's own areas to crack in, mostly around the air ducts. Fortunately, it is a floating floor, meaning the walls set on the foundation, not the floors, so the cracks do not affect functionality. They sure are ugly though.


This last picture shows the wooden window frame with the rolling shutter installed. We chose this type of covering for it's security and safety aspects, as well as the fact it can be retracted from inside the house. We also chose a manual mechanism to avoid loosing function if the power went out. We have one of these on each window, and each door.







Sunday, August 16, 2009
3rd and Final Module





Friday, August 14, 2009
More Terra-Dome Pictures
These pictures show the concrete pumping for the 2nd module. I took the day off from work so I could watch them. It was really fascinating to watch.

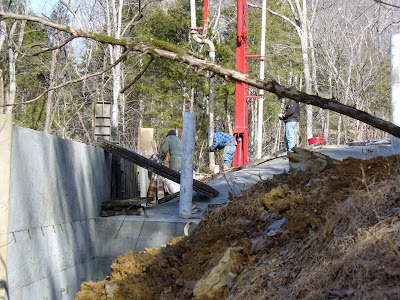


This is the pumper truck that moved the concrete up to the roof. Unfortunately, it kept getting clogged and as a result, we had several concrete trucks backed up, allowing the concrete to get old. It made the final product a little rough, but the strength was unaffected.


Here is the beginning of the 3rd module. The front wall forms are not installed yet and this allows a great view of the dome structure.
This is the pumper truck that moved the concrete up to the roof. Unfortunately, it kept getting clogged and as a result, we had several concrete trucks backed up, allowing the concrete to get old. It made the final product a little rough, but the strength was unaffected.
Here is the beginning of the 3rd module. The front wall forms are not installed yet and this allows a great view of the dome structure.

Sunday, August 9, 2009
Construction Begins in Earnest
One of the biggest problems with building an unusual house is getting the financing. Traditional mortgage sources won't touch anything that doesn't look like every other house in the neighborhood. It took us several years, but we finally found a small, local bank that will lend money for anything if you have the credit, but of course it costs more. We have had to pay about 3-4 percentage points above the normal mortgage rates, but as our banker is found of saying "It's a small price for your dream home".
One of the things we did was to visit the Terra-Dome folks and look at several houses they built in the area. We actually traveled up to Missouri twice to gather as much information as we could. Of course, even that was not enough to avoid mistakes, but I think it did help a lot.
Anyway, once the plans were finalized, the construction loan secured, and the contract signed, we began to build in earnest (hence the title). I was glad to be able to finally answer the constant question from friends "So when are you going to get started on that underground house of yours?" with the reply "We have the contractor out there right now".


I missed the first few days of building because I was on a trip, but when I returned, this is what I found. A few things to note about the construction of a Terra-Dome house. Because of the tremendous weight of the building and the dirt on top, the footings are extra wide, as you can see under the ladder in the picture above. Also, with each module, there must be a 9 foot opening to allow the forms that create the domed roof to be removed once the concrete has set. This takes about 3 days. These openings must be accounted for in the plans, but as you will see later, they can be filled in during the later construction phases.

This is a shot of the interior, showing the supports the hold up the dome forms.

This view shows the footing for the next module. The grooves are to allow electrical outlets in the wall to be connected under the floor before it is poured.


These views shows the forms for the 2nd module adjacent to the completed first module. Notice the opening on the right for the master bath window, and the front door in the 2nd module.

Here is more detail of the front door.
You can see the dome form on top. There is lots of rebar in these buildings, especially in the roof. They use a very specific pattern to ensure the engineering requirements have been met.
One of the things we did was to visit the Terra-Dome folks and look at several houses they built in the area. We actually traveled up to Missouri twice to gather as much information as we could. Of course, even that was not enough to avoid mistakes, but I think it did help a lot.
Anyway, once the plans were finalized, the construction loan secured, and the contract signed, we began to build in earnest (hence the title). I was glad to be able to finally answer the constant question from friends "So when are you going to get started on that underground house of yours?" with the reply "We have the contractor out there right now".


I missed the first few days of building because I was on a trip, but when I returned, this is what I found. A few things to note about the construction of a Terra-Dome house. Because of the tremendous weight of the building and the dirt on top, the footings are extra wide, as you can see under the ladder in the picture above. Also, with each module, there must be a 9 foot opening to allow the forms that create the domed roof to be removed once the concrete has set. This takes about 3 days. These openings must be accounted for in the plans, but as you will see later, they can be filled in during the later construction phases.

This is a shot of the interior, showing the supports the hold up the dome forms.

This view shows the footing for the next module. The grooves are to allow electrical outlets in the wall to be connected under the floor before it is poured.


These views shows the forms for the 2nd module adjacent to the completed first module. Notice the opening on the right for the master bath window, and the front door in the 2nd module.

Here is more detail of the front door.

Sunday, August 2, 2009
It all started with an idea.
I'm going to go back in time to about 10 years ago. We attended Education Week at Brigham Young University with our best friends, John and Lorraine Thiele, and while we were there, we felt we needed to move out of our current house and into something that would protect us from as many possible disasters as we could think of. We were concerned about floods, tornadoes, lightning, power outages, termites, and looters. A pretty tall order, but we set out doing research. I found a lot of information on the web and started putting my ideas together. We realized an underground, or earth bermed, concrete house would probably take care of all of our issues, so I concentrated on that. I was also hoping to be able to do a lot of the work myself to try and save money.
We narrowed our search to 3 builders, each with a different style of concrete home. We first saw Davis Caves. They build home that look pretty much like regular houses on the inside, except that in order to hold up their flat concrete roofs, you need a support pole every 8 feet. This seemed to limit our layout options too much, and they felt a little cramped, so we went to the next option. Monolithic Domes are round structures with dome ceilings that feel very roomy, but adapting to round walls is not very practical. It was also not designed for being completely buried, so we rejected that also. Finally we checked out Terra-Dome. It seemed to be the perfect combination of square walls and a domed roof. Check out their website for more details (terra-dome.com).


Next came the layout. We struggled with this for more than 2 years. Terra-Dome (TD) homes have 2 basic options, with endless possible combinations; a 24 x 24 module, or a 28 x 28 module. you can put as many of these together as you want, in just about any configuration. We finally submitted the plans below to TD for a quote and we thought we were on our way.
While we were working on the plans we looked for a place to build. Let's just say providence smiled on us and we were able to buy 5.6 acres with a nice hill to build into at auction for just $18,500. These pictures were taken just after the driveway was put in.



Having a solid plan, we went ahead and had the excavation work done to prep the site. Here is how that looked.


That's enough for now. I will add more about the building process next time.
We narrowed our search to 3 builders, each with a different style of concrete home. We first saw Davis Caves. They build home that look pretty much like regular houses on the inside, except that in order to hold up their flat concrete roofs, you need a support pole every 8 feet. This seemed to limit our layout options too much, and they felt a little cramped, so we went to the next option. Monolithic Domes are round structures with dome ceilings that feel very roomy, but adapting to round walls is not very practical. It was also not designed for being completely buried, so we rejected that also. Finally we checked out Terra-Dome. It seemed to be the perfect combination of square walls and a domed roof. Check out their website for more details (terra-dome.com).


Next came the layout. We struggled with this for more than 2 years. Terra-Dome (TD) homes have 2 basic options, with endless possible combinations; a 24 x 24 module, or a 28 x 28 module. you can put as many of these together as you want, in just about any configuration. We finally submitted the plans below to TD for a quote and we thought we were on our way.

Having a solid plan, we went ahead and had the excavation work done to prep the site. Here is how that looked.


That's enough for now. I will add more about the building process next time.
Subscribe to:
Posts (Atom)